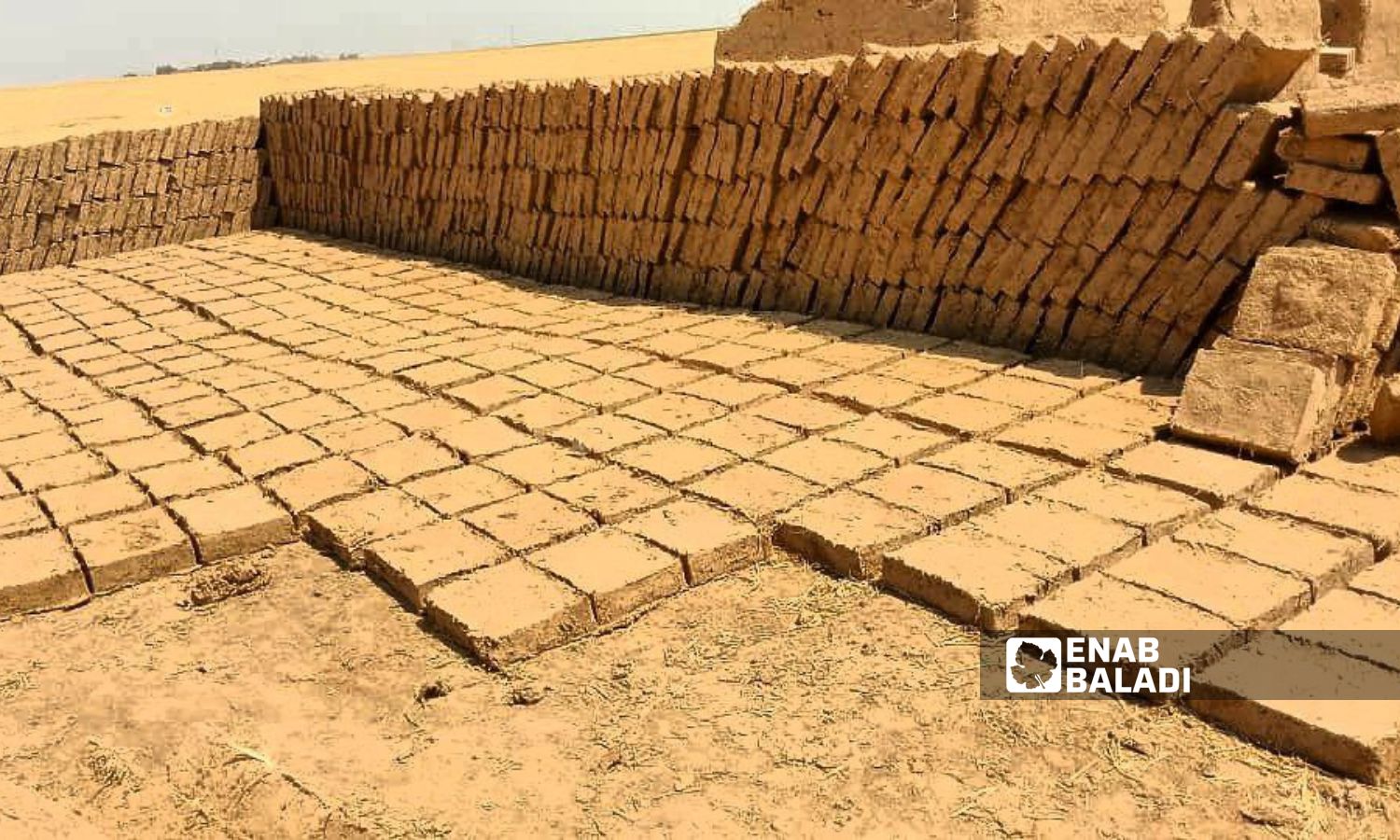
Mud bricks ready for sale in rural Qamishli - August 20, 2024 (Enab Baladi)
Mud bricks ready for sale in rural Qamishli - August 20, 2024 (Enab Baladi)
Qamishli – Majd al-Salem
Amidst the rising costs of conventional building materials like concrete blocks in al-Hasakah, villagers in the countryside have turned to mud bricks as an economical and sustainable alternative.
Constructing homes using mud bricks is one of the oldest building methods in the region, but its resurgence today is a response to economic challenges and the need for solutions that are more in harmony with the extremely hot summers and cold winters of the surrounding environment.
After building a cement house about six years ago in his village of Khuwaytla, rural Qamishli, Mohammad al-Hussein decided to build a mud room similar to a guest room in front of his cement house.
The sixty-something-year-old told Enab Baladi that he couldn’t tolerate the heat of the cement house in the summer or its coldness in the winter; it would turn into an “icebox” in the winter and a “furnace” in the summer.
The heat was exacerbated by power outages in the countryside, with electricity being available only one hour every 24 hours, making it difficult to rely on it to mitigate the heat of the cement house.
Al-Hussein added that the mud house has excellent thermal insulation, and a battery-operated fan is enough to achieve acceptable coolness, especially if the floors are also made of mud without using cement or tiles.
He mentioned that when the floor is sprinkled with water while a regular fan is running, the room becomes cool in summer. In winter, even a small heat source makes the family feel warm, as the hot air remains longer even after turning off the heater.
Reacting to the scarcity and high costs of energy sources like diesel and electricity, many, like al-Hussein, have built isolated mud rooms from their cement buildings to take advantage of their high thermal insulation.
The cost of mud bricks cannot be compared to that of cement bricks (blocks). The former is very cheap and accessible to everyone. This is confirmed by Walid al-Habeeb (34 years old) from rural Qamishli, who owns a workshop producing and selling mud bricks, locally known as “al-liben.”
Al-Habeeb said that mud bricks are made from cheap, locally available raw materials, which are earth and straw mixed together. Water is added in a specific quantity, and the mixture is left to “rest” until the next day.
Water is then added again, and the components are well mixed and kneaded using a shovel and feet to achieve a specific consistency. The resulting clay is poured into rectangular wooden molds with dimensions of 40×30 centimeters and a specific thickness (called al-Malban). These molds are left under the sun to dry for two or three days, after which they are ready for building.
Production of mud bricks requires no machinery or electrical tools, just water and expertise.
Regarding the prices, al-Habeeb stated that he does not sell in dollars as cement brick factories do but in Syrian currency, which has increased the demand for mud bricks.
Al-Habeeb sells each thousand mud bricks for 1,300,000 Syrian pounds ($84), while a thousand cement blocks are sold for $450 (6,975,000 Syrian pounds).
He believes that the prices lower the construction cost of a house to less than a quarter compared to building with cement, thus there is a demand for this type of building amidst the harsh economic conditions and lack of job opportunities in the countryside.
Dozens, if not hundreds, of mud-brick houses have been built by Mohammad Abbas (47 years old) from rural Qamishli, during the current year and previous years, ever since he began his profession as a builder, locally known as “al-Mu’amer.”
Abbas told Enab Baladi that there is a demand for this type of building mainly due to its very low cost, with some people building their entire house with mud bricks.
He added that others, who own cement houses and are well-off, request the construction of a separate mud-brick room away from the house.
He mentioned that there are several types of “developed” mud brick houses nowadays or houses incorporating both mud bricks and cement blocks.
Some houses are entirely built from mud bricks and require periodic maintenance before each winter. Others are built up to a quarter or halfway (half the height of the walls) with cement blocks for stronger foundations, and then the rest of the walls are completed with mud bricks.
The best type, according to Abbas, is building the entire house from mud bricks and then encasing the mud walls with another cement block wall. This type needs no maintenance and has very high thermal insulation.
Abbas noted that the type of soil and the amount of straw added to the mud significantly affect the brick’s quality and durability. The best soil comes from the southern region of al-Radd, in the far southern countryside of Qamishli near the Iraqi border, as it produces highly durable bricks with a whitish hue.
if you think the article contain wrong information or you have additional details Send Correction